FREQUENTLY ASKED QUESTIONS
Here are a few questions that we are asked, and that may be of help to you. If you would like to contact us or speak to us, please call 0330 350 0715.
Who are THINK inventory solutions?
THINK Inventory Solutions are one of the UK’s leading software houses specialising in Warehouse Management Systems (WMS). We have been in the software industry for over fifteen years and have over 100 years of warehouse management experience including leading one of the world’s biggest automotive tier one suppliers at GM level.
What is a warehouse management system (WMS)?
A warehouse management system or WMS is a software solution that helps businesses optimise their warehouse operations. With the help of a warehouse management system (WMS) you can track your inventory, manage orders, and automate key tasks.
What does a warehouse management system do?
The software and processes within a warehouse management system or WMS allows the business to streamline each step of their warehouse operation. From receipt of goods, stock control and visibility, to storage, picking, packing, shipping and everything in between.
What are the functions of a warehouse management system?
The key functions of THINK’s warehouse management system or WMS include
ASN – Advanced Shipping Notices
THINK WMS can receive and transmit ASN’s in many formats including VDA, EDIFACT, xml and many more. Ensuring you and your business partners benefit from the latest in EDI standards. Receiving Our fully configurable receiving process provides full flexibility allowing you to tailor your processes to your requirements.
Stock Control and Visibility
Stock balances and status can be viewed at multiple levels and locations with a full history provided at handling unit level. Warehouse capacity reporting can be tailored to your individual requirements.
Demand Fulfilment
Managing customer requirements from multiple sources efficiently and effectively is pivotal to any WMS. Our WMS provides full visibility of the status of all requirements allowing the user to prioritise as and when required, with configurable pick options.
Despatching (Shipping)
Accuracy and efficiency are key drivers in any shipping process. THINK process templates offer full configuration options to meet all requirements.
Serial Tracking
Do you need to track inventory at component or package level? Do you supply safety critical products or have high warranty costs to be monitored. Our serial tracking module is packed with features that provide full traceability at unit level if required.
Traceability
Full traceability can be supported from individual unit level, if required, to handling unit and from receipt to despatch offering you full scope to meet your existing, and future, customer requirements.
Specialised Functionality
THINK have provided solutions across a wide range of industries and can offer functionality in electronic Kanban, work orders, automotive sequencing and many more. Get in touch to find out how we can help you save money and gain greater efficiencies.
What are the benefits of a warehouse management system (WMS)?
Investing in a warehouse management system from THINK can make a huge difference to your operation. Our software can give you greater accuracy and transparency of inventory and can even help you reduce costs and improve your supply chain.
Here are some of the key features of an effective inventory management system:
- Warehouse Management
- Stock Notifications
- Inventory Optimisation
- Warehouse Scanning Systems
- Report Generation
- Sales Analysis
When do you need a warehouse management system and why?
A warehouse management system or WMS is required when a business operates a warehouse or distribution centre with inventory that needs to be managed efficiently and accurately. A warehouse management system or WMS can help streamline operations and increase productivity by automating processes such as inventory tracking, order fulfillment and shipping. Implementing a warehouse management system or WMS can be a valuable investment for businesses looking to optimise their warehouse or distribution centre operations and improve customer satisfaction.
How much does a warehouse management system cost?
Implementing a Warehouse Management Software is a significant investment for many organisations and there are normally a number of expected outcomes, improved efficiency, better stock accuracy, improved picking accuracy and efficiency, improved customer satisfaction etc. The cost of a warehouse management system (WMS) itself can vary significantly depending on various factors, including the size and complexity of your warehouse operations, the features and functionalities you require. THINK make it our mission to understand the implementation, scope and objectives of your businesses needs and provide a tailored quotation based on your individual requirements.
Will a warehouse management system integrate with my existing warehouse systems and processes?
THINK’s Warehouse Management System is designed to easily interface with other business applications ranging from ERP systems such as SAP, System 21, SAGE, MS Dynamics, Oracle etc. Through to Ecommerce providers such as Shopify & Prestashop.
How does a warehouse management system support omnichannel retail strategies?
A warehouse management system can support omnichannel retail strategies in several ways. Firstly, a WMS can help retailers optimise inventory management across multiple channels, ensuring that inventory levels are balanced and that products are available where and when customers what them. Secondly, a WMS can help retailers improve order accuracy and speed, enabling them to fulfill orders more quickly and efficiently. Thirdly, a WMS can provide real-time visibility into inventory levels and order status across all channels, allowing retailers to make informed decisions about where to allocate stock and how to fulfill orders. Finally, a WMS can help retailers reduce costs by optimising warehouse operations, reducing errors and improving efficiency.
Overall, a WMS plays a crucial role in supporting omnichannel retail strategies, helping retailers to meet customer expectations for speed, accuracy, and convenience while also improving operational efficiency and reducing costs.
How does warehouse management affect supply chain management?
Effective warehouse management can have a significant impact on supply chain management. A well-managed warehouse can help improve inventory accuracy, reduce lead times, increase order fulfillment rates, and enhance customer satisfaction. Additionally, warehouse management can help optimise the flow of goods through the supply chain, reducing costs and improving efficiency.
How does a warehouse management system improve order accuracy and customer satisfaction?
A warehouse management system can improve order accuracy and customer satisfaction in several ways. A WMS can help automate and optimise the order fulfillment process, reducing errors and increasing accuracy. Improving inventory visibility, providing real-time information on inventory levels and locations, can help reduce stock shortages and improve order fulfillment rates. By improving warehouse efficiency and the reduction of processing times, it enables faster fulfillment and delivery. A WMS can provide real-time tracking and visibility of orders, allowing customers to track their own orders and receive timely updates, which in turn improves customer satisfaction.
What factors should be considered when choosing a warehouse management system?
When choosing a warehouse management system or WMS several factors should be considered to ensure that the system meets the needs of the business. These factors include:
Scalability
The WMS should be scalable to accommodate the current and future needs of the business.
Ease Of Use
The system should be user-friendly and easy to navigate to ensure that employees can quickly learn and use the system.
Integrations Capabilities
The WMS should integrate with other systems such as ERP to ensure seamless data flow across the supply chain.
Customisation
One size does not fit all; the WMS therefore should be able to be customized to the specific needs of the business
Real-time Visibility
The system should provide real-time visibility into inventory levels, order status, and order critical data to ensure that businesses can make informed decisions.
Cost
The cost of the WMS should be considered, including roll out, implementation, maintenance and training costs.
Support
Perhaps the most important of all the WMS vendor should provide reliable and responsive support to ensure that any issues are quickly resolved.
Considerations when designing an effective fulfilment process
Considerations when designing an effective fulfilment process.
- Product characteristics: Different types of products have varying characteristics that require specific handling procedures. For example, fragile items may need extra care in packaging and shipping, perishable goods may require temperature-controlled storage and transportation, and hazardous materials have strict safety regulations.
- Storage requirements: Products with different storage requirements may need separate handling and storage arrangements. For instance, bulky or oversized items might require dedicated storage space, while temperature-sensitive products may require specialized climate-controlled areas.
- Order volume: The volume of orders can significantly impact fulfilment processes. High-volume operations may require efficient picking and packing strategies, automation, and streamlined workflows to meet demand and maintain quick turnaround times.
- Order complexity: The complexity of orders can also affect fulfilment processes. Some products may have multiple components or require assembly before shipping. These factors can influence the organization of inventory, picking methods, and packaging procedures.
- Order prioritisation: Depending on the nature of the products and customer requirements, certain orders may need to be prioritized over others. For example, expedited shipping may be necessary for time-sensitive goods, while different shipping methods may be appropriate for different product types.
- Returns and exchanges: The handling of returns and exchanges may vary based on the type of product. Some items may need inspection or testing before reshelving, while others may require specific return procedures due to regulatory or quality control reasons.
To optimize efficiency and ensure customer satisfaction, warehouses often customize their fulfilment processes to accommodate these factors and achieve effective operations specific to the products they handle.
Do you need help?
Are you worried that a Warehouse Management solution will cost you loads of money? Or you will be trapped in a long contract?
Give THINK a call on 0330 350 0715 we can work with your business to help save you money and drive down costs!
Third Party Logistics
We recognised early on with our first 3PL customers coming on board that this industry sector had significantly different drivers to other industries.
Automotive & Manufacturing
We can offer truly unique and fully integrated solutions for managing and controlling your inventory from dispatch of product.
Warehouse & Distribution
Think WMS has evolved to support the specialised requirements of a number of clients within the food industry.
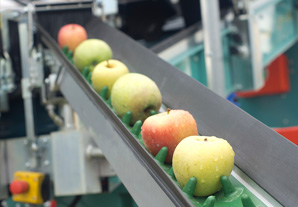
Food
In the highly competitive and diverse market of warehouse and distribution you require flexible solutions to the requirements of your customers, THINK WMS is that product.
Are you worried that a warehouse management solution will be too expensive, or that you will be trapped in a long contract? To arrange a demo or discuss your requirements, give THINK a call on 0330 350 0715, email enquiries@tkinv.com or complete the Quick Quote form below. We can work with your business to help save you money and drive down costs.